What is Porosity in Welding: Recognizing Its Reasons and Enhancing Your Abilities
Wiki Article
The Science Behind Porosity: A Comprehensive Overview for Welders and Fabricators
Understanding the detailed systems behind porosity in welding is crucial for welders and makers pursuing remarkable craftsmanship. As metalworkers look into the depths of this sensation, they reveal a world controlled by different factors that influence the formation of these minuscule spaces within welds. From the composition of the base materials to the complexities of the welding procedure itself, a multitude of variables conspire to either exacerbate or relieve the existence of porosity. In this extensive guide, we will certainly unwind the science behind porosity, exploring its effects on weld top quality and introduction advanced strategies for its control. Join us on this trip with the microcosm of welding imperfections, where accuracy satisfies understanding in the pursuit of remarkable welds.Understanding Porosity in Welding
FIRST SENTENCE:
Assessment of porosity in welding reveals critical insights right into the stability and top quality of the weld joint. Porosity, defined by the visibility of tooth cavities or gaps within the weld metal, is an usual worry in welding processes. These spaces, otherwise properly resolved, can compromise the structural stability and mechanical residential properties of the weld, leading to potential failures in the ended up product.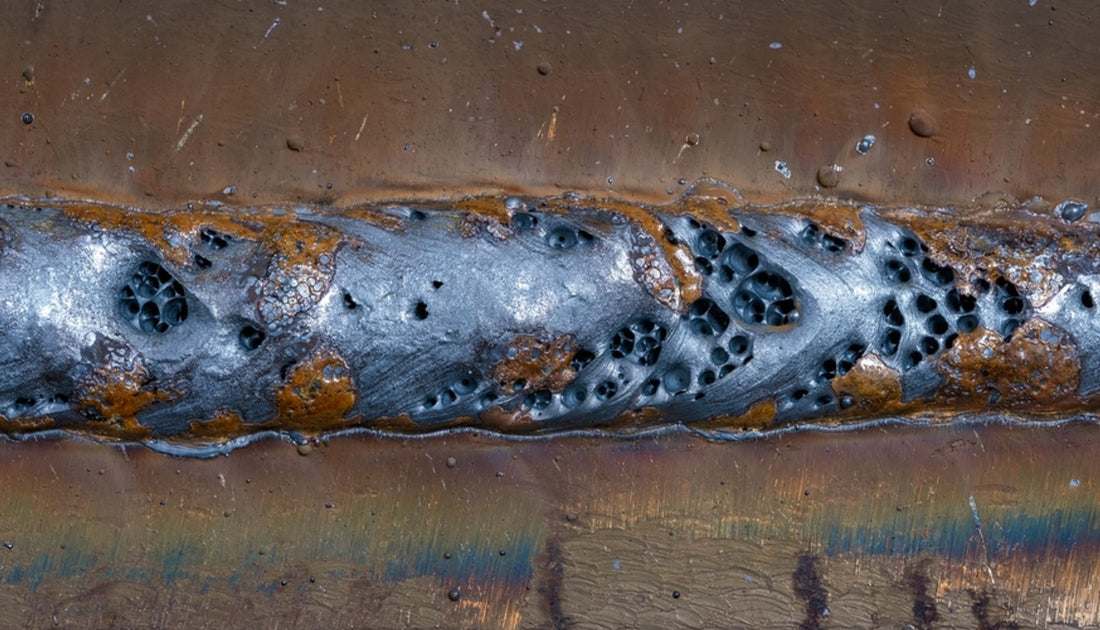
To detect and quantify porosity, non-destructive screening approaches such as ultrasonic screening or X-ray inspection are often used. These methods enable the identification of inner flaws without endangering the honesty of the weld. By assessing the size, form, and distribution of porosity within a weld, welders can make educated choices to improve their welding procedures and accomplish sounder weld joints.
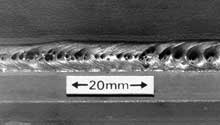
Aspects Influencing Porosity Development
The occurrence of porosity in welding is influenced by a myriad of factors, ranging from gas securing effectiveness to the ins and outs of welding specification settings. One critical factor contributing to porosity formation is poor gas shielding. When the securing gas, typically argon or carbon dioxide, is not successfully covering the weld pool, atmospheric gases like oxygen and nitrogen can pollute the molten steel, leading to porosity. Furthermore, the cleanliness of the base products plays a substantial function. Contaminants such as corrosion, oil, or dampness great post to read can vaporize during welding, producing gas pockets within the weld. Welding criteria, consisting of voltage, present, take a trip rate, and electrode type, additionally influence porosity development. Utilizing inappropriate settings can generate excessive spatter or heat input, which consequently can result in porosity. Furthermore, the welding technique employed, such as gas metal arc welding (GMAW) or protected steel arc welding (SMAW), can influence porosity development as a result of variations in heat distribution and gas protection. Understanding and controlling these variables are vital for minimizing porosity in welding procedures.Effects of Porosity on Weld Top Quality
Porosity formation significantly compromises the architectural integrity and mechanical properties of welded click here for more info joints. When porosity exists in a weld, it creates spaces or dental caries within the material, lowering the total toughness of the joint. These spaces act as tension concentration points, making the weld a lot more prone to cracking and failure under lots. The presence of porosity also compromises the weld's resistance to deterioration, as the caught air or gases within the spaces can react with the surrounding atmosphere, bring about destruction over time. In addition, porosity can hinder the weld's capacity to endure pressure or effect, additional threatening the general quality and integrity of the bonded structure. In essential applications such as aerospace, automobile, or structural buildings, where security and longevity are vital, the destructive impacts of porosity on weld top quality can have severe effects, emphasizing the relevance of minimizing porosity through appropriate welding strategies and treatments.Techniques to Minimize Porosity
Additionally, utilizing the proper welding specifications, such as the correct voltage, current, and take a trip rate, is crucial in preventing porosity. Maintaining a regular arc size and angle throughout welding additionally assists decrease the likelihood of porosity.
Utilizing the appropriate welding technique, such as back-stepping or utilizing a weaving motion, can likewise assist distribute warm uniformly and minimize the opportunities of porosity development. By carrying out these strategies, welders can effectively reduce porosity and produce premium welded joints.
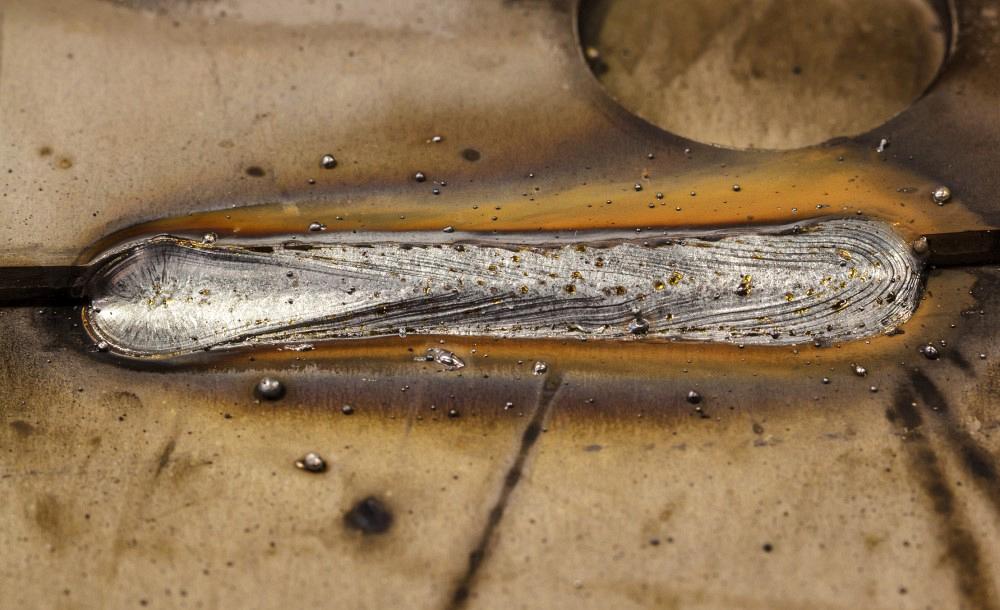
Advanced Solutions for Porosity Control
Applying innovative technologies and innovative techniques plays a critical function in accomplishing remarkable control over porosity in welding processes. One advanced service is using innovative gas blends. Shielding gases like helium or a mixture of argon and hydrogen can help in reducing porosity by giving much better arc stability and enhanced gas insurance coverage. In addition, using advanced welding methods such as pulsed MIG welding or modified atmosphere welding can additionally assist minimize porosity problems.An additional sophisticated option involves using advanced welding equipment. As an example, using equipment with integrated features useful content like waveform control and sophisticated source of power can boost weld quality and decrease porosity risks. The application of automated welding systems with precise control over parameters can considerably lessen porosity defects.
Moreover, integrating sophisticated tracking and assessment modern technologies such as real-time X-ray imaging or automated ultrasonic screening can help in identifying porosity early in the welding process, permitting for immediate rehabilitative activities. Generally, integrating these advanced services can significantly improve porosity control and improve the overall high quality of bonded components.
Final Thought
In conclusion, understanding the science behind porosity in welding is necessary for welders and fabricators to create high-grade welds - What is Porosity. Advanced options for porosity control can additionally improve the welding procedure and make sure a strong and dependable weld.Report this wiki page